
There are several regulatory standards mandating the use of rubber insulating equipment to protect workers from arc flash and electrical hazards. Regardless of the heavy fines, serious injuries, and deaths that occur from electrical incidents, compliance continues to remain an issue. What is even more shocking is that many workers are not using rubber insulating equipment because they do not know they need it, or because they are unsure of how to select the proper personal protective equipment (PPE) for the application.
In reality, almost every single facility has a need for arc flash and electrical safety – whether the company is a larger facility with building engineers overseeing distribution, or a smaller facility with maintenance staff working on or around floor or wall sockets. There is quite a large number of possible end users. As such, awareness is paramount. Not only about the requirements for use, but also about for how to choose the right rubber insulating equipment to protect workers and employers against injury, loss time, costly damage, legal liability, increased insurance premiums, and hefty regulatory fines.
While the best way to prevent arc incidents from happening is through engineering controls such as de-energizing equipment before beginning work, there are instances where turning off the power could create an even greater hazard. Therefore, employers and facility owners must establish safe practices to protect their workers against arc flash incidents including the use of PPE. The NFPA, along with the Occupational Safety and Health Administration (OSHA), mandates and enforces safer electrical work practices under the NFPA 70E standard. Numerous experts and training programs are available to provide guidance on how to keep workers safe and compliant in terms of conducting a proper arc flash hazard analysis. The results of the analysis will usually guide the property owner regarding the controls that should be in place (engineering, mechanical, human, or otherwise) and review the hazards of both arc flash and electrical shock. From there, proper PPE options ―such as arc-rated clothing ― can be determined. However, one topic that is often not discussed in detail is the need for rubber insulating gloves where a shock hazard exists from exposure to energized equipment.
Gloving Your Hands
Employees that work on electrically energized circuits and equipment use their hands, making them the most susceptible part of the body to electric shock. Arc-rated work gloves offer no shock protection, and most arc flash hazards have a shock flash hazard as well. Rubber insulating gloves (electrical gloves) are an essential element in protecting workers that are exposed to high-voltage currents. Shock protection is the primary benefit. However, electrical gloves also provide significant burn protection in the event of an arc flash. Electrical gloves are manufactured using proprietary materials and manufacturing processes with 100% testing to provide the highest possible level of protection. To be effective, electrical gloves must incorporate high dielectric and physical strength along with comfort, flexibility, and durability. To help ensure safety and performance, they should meet and/or exceed the requirements of ASTM D120 Standard Specification for Rubber Insulating Gloves.
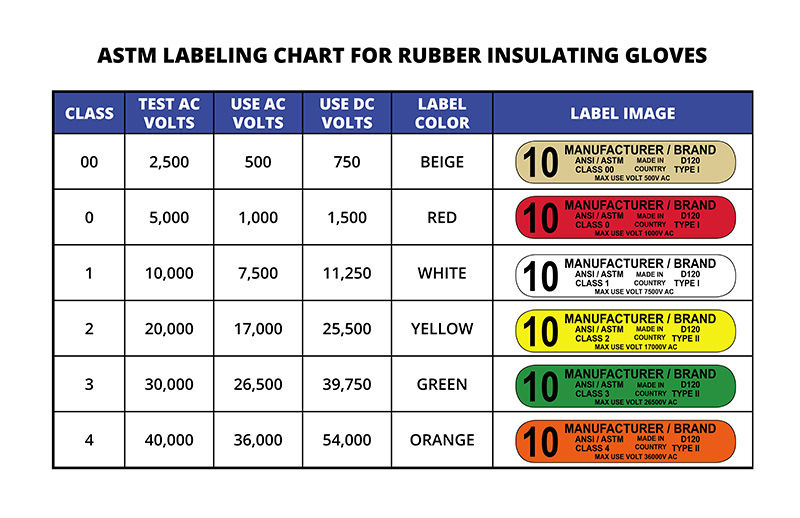
OSHA rules and the NFPA 70E standard require the use of rubber insulating products when even the smallest probability of contact with 50 volts AC or higher exists. According to the OSHA 29 CFR 1910.137 standard, electrical gloves must be rated for the voltage to which a worker will be exposed (phase to ground or phase to phase) and marked to indicate their rating. For in-service use, the maximum-use voltage must be above the actual exposure, but it is important to take note of the proof-test voltage as well. Electrical gloves are offered in six different voltage rating “classes,” based on ASTM D120. All electrical gloves are tested by the manufacturer at the specified proof test voltage.
Manufacturers also perform a dielectric breakdown test at an even higher voltage to validate the dielectric strength of the rubber material. The result is a significant margin of safety between the proof-test voltages and the maximum-use voltage. Each specific hazard assessment will help you determine which class of electrical gloves is appropriate for your application.
Electrical gloves are categorized by the level of voltage protection they provide. Voltage protection is broken down into classes, and each class of gloves is clearly marked with the maximum-use voltage on the permanent color-coded label (see chart).
Take care to choose the right glove size, as proper fit will ensure the likeliness that the workers will wear the electrical gloves. Gloves that are too big or bulky can affect tactile sensitivity, while gloves that are too small can cause discomfort. ASTM D120 section 8.2 provides the measurements of the diameter of the palm for manufacturers, measured at the midpoint of the palm, plus or minus a ½ inch. Measure the hand by wrapping the tape all the way around the palm. This number would equate to the probable size of the glove to select. Personal preference for tightness and finger length will ultimately determine the size that the wearer will choose. Electrical gloves are typically manufactured in sizes 8-12, often in ½ sizes, and some manufacturers also offer gloves as small as size 7 and as large as size 13. In addition, electrical gloves are available in different cuff lengths of 11, 14, 16, and 18 inches depending on the glove class.
Protecting the Gloves that Protect You
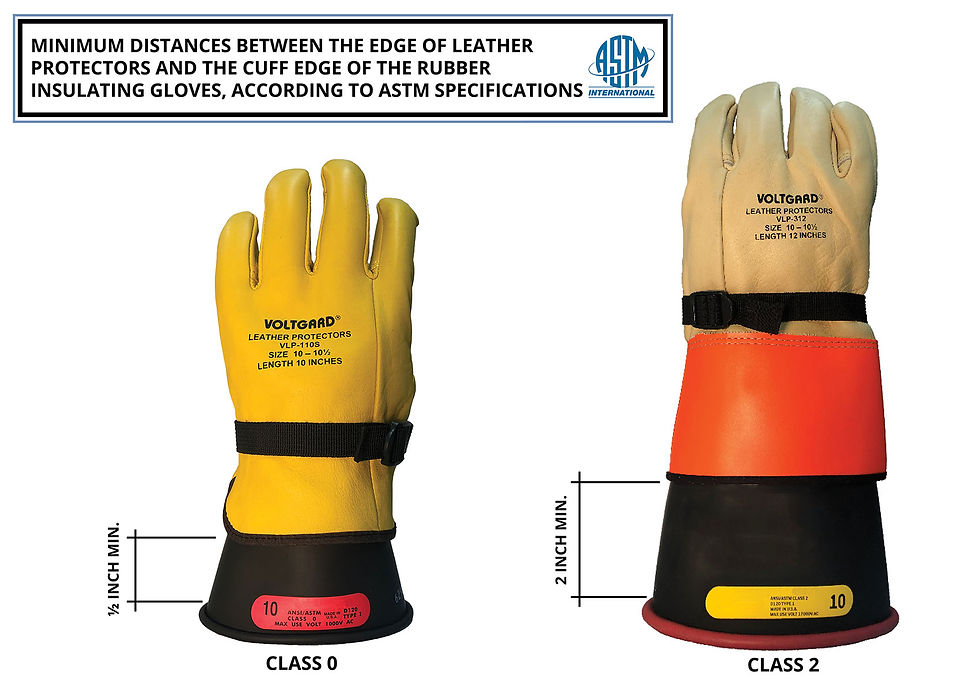
With few specific exceptions, electrical gloves must always be worn with leather protector gloves manufactured in compliance with ASTM standard specification F696. The OSHA “269” standard (29 CFR 1910.269) requires that rubber insulating gloves along with leather protectors must be worn by qualified employees within the Minimum Approach Distance (MAD) to exposed energized conductors. That being said, equal care and consideration should also be given when selecting the appropriate leather protector gloves. Leather protector gloves are worn over electrical gloves to extend their life and provide protection to the gloves from cuts, abrasions, and punctures. Use the ASTM F696 standard specifying the types of materials, construction, and other details as a guide in the selection process. Keep in mind that there is a tracking and flashover risk which increases as the voltage potential increases. Since the materials in the leather protector gloves have no dielectric properties and may absorb moisture or at least track electricity, it is important to maintain a gap between the leather protector glove and the wearer’s body parts, like the hand and arm. Therefore, the leather protector must be shorter than the rubber glove so that there is exposed rubber as a line of defense against tracking and flashover. The applicable ASTM specifications state that the minimum distance between the edge of the leather protector and the cuff edge of the rubber insulating glove is ½ inch for low-voltage gloves and 1 inch per glove class for high-voltage gloves. Knowing this, the leather protector for a Class 2 electrical glove must be at least 2 inches shorter than the rubber glove.
All in all, electrical gloves are a necessary component to most worker safety programs, as they are the only protective gear designed for constant contact with, and protection from, energized conductors and equipment. All other items are designed for protection from accidental, incidental, or brush contact. Consequently, choosing the correct electrical gloves (and leather protector gloves, too) using the ASTM specifications and standards for class and materials, as well as hand measurements and sizes is key to ensuring worker safety.
Reblogged from ElectricalSafetyPub.com: Richard Rivkin; https://www.electricalsafetypub.com/features/how-to-choose-the-right-electrical-gloves-for-the-task-at-hand/
Comments